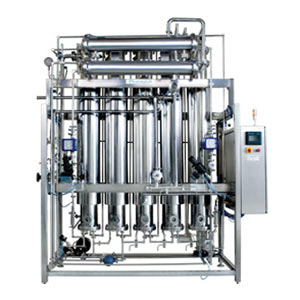
WFI ژنراتور
WATER FOR INJECTION
BACKGROUND
Water for Injection (WFI) international pharmacopoeial standards have been brought closer through harmonization efforts, but significant differences still exist. The USP WFI monograph allows production by “distillation or a purification process proven to be equal to or superior to distillation.” USP language is the least restrictive in terms of acceptable processes among the major pharmacopoeial groups. The Japanese Pharmacopeia (JP) allows distillation, or reverse osmosis (RO) followed by ultrafiltration (UF). Distillation is the only WFI method of production that is approved by the European Pharmacopoeia (EP).
Historically, distillation has been the preferred method for producing WFI in the biopharmaceutical industry, and today, most pharmaceutical WFI is produced by distillation. Regulatory requirements have helped significantly in the domination of WFI production by distillation, but distillation has also been successful in attainment of the water quality specifications. Yet, most other high-purity industries use reverse osmosis, deionization and ultrafiltration, not distillation, to produce WFI equivalent or higher quality water. Type A laboratory water limits for total bacterial count and endotoxin are respectively ten and eight times lower than WFI. ASTM Type 1.2 water for microelectronics has similar microbial restrictions with total organic carbon and conductivity limits well below WFI. Those applications are routinely satisfied with membrane-based systems producing water at ambient temperature. Those industries, however, do not have regulated process limitations
DISTILLATION BASED WFI SYSTEMS
To meet USP requirements, WFI must be produced by “distillation or a purification process proven to be equal to or superior to distillation.” Additionally, the water must pass conductivity and total organic carbon (TOC) tests, and the bacteria endotoxin level must be below 0.25 endotoxin units per milliliter (EU/mL). The microbial level must not be above 10 colony-forming units (CFU) per 100 mL. Distillation is effective at quantitative reduction of most water contaminants and can produce water with low conductivity, low TOC, low microbial levels and low endotoxin levels.
Almost all pharmaceutical distillation based systems implement either multiple effect or vapor compression stills. Both still types employ various techniques for recovery of latent and sensible heat to minimize energy consumption. Both technologies produce WFI quality water when properly implemented and operated. Each still type has advantages and disadvantages and each has significant successful operational history.
While stills are reliable, they are not perfect, and can produce pyrogenic product water when operated incorrectly, when they fail mechanically or when the feed water contains contaminant levels beyond the still reduction capability. If fed with high endotoxin feed water from the raw supply or pretreatment equipment, in cases where there is no membrane based system pre-treating the still, the product water from the still may fail the endotoxin test. Many successful distillation systems exist with no membrane pretreatment, but several other systems have required retrofit of reverse osmosis (RO) or ultrafiltration (UF) pretreatment after periodic product water endotoxin failures due to high still feed endotoxin levels.
The FDA Guide for Inspections of High-Purity Water Systems recognizes the still pretreatment design question regarding potential use of a membrane process. Section V of the Guide states, “Many of the still fabricators will only guarantee a 2.5-log to 3-log reduction in the endotoxin content. Therefore, it is not surprising that in systems where the feed water occasionally spikes to 250 EU/mL, unacceptable levels of endotoxins may occasionally appear in the distillate (WFI). For example, three new stills, including two multi-effect, were recently found to be periodically yielding WFI with levels greater than 0.25 EU/ml.”
The FDA Guide further states, “Pre-treatment systems for the stills included only deionization systems with no RO, ultrafiltration or distillation. Unless a firm has a satisfactory pre-treatment system, it would be extremely difficult for them to demonstrate that the system is validated.” The decision to implement or not implement reverse osmosis in still pretreatment is generally more relevant to vapor compression stills than multiple effect stills. Vapor compression stills operate at a necessary for scale and corrosion prevention. Multiple effect stills generally require feed water with low levels of chloride, silica and total solids and are almost always pretreated with reverse osmosis and/or an ion exchange process. Since reverse osmosis is present in almost all ME still feed systems, the feed endotoxin levels are quite low.
WHAT OTHER TREATMENT METHODS WORK?
A number of separation methods, such as RO and UF, can remove endotoxin. Oxidation with ozone also removes endotoxin. Heat, distillation, UF, RO, filtration, ozone, UV and chemical methods can all achieve low microbial levels in the product water. Other market applications such as microelectronics and select laboratory water types have water quality specifications far tighter than WFI including extremely low endotoxin limits. Almost all of these systems utilize membrane technologies for primary treatment. Membrane systems may offer lower operating economics as no water evaporation occurs. Systems either operate at ambient temperature normally or are heated to high temperature without evaporation and condensation. The content of stainless steel is often less with membrane systems compared to distillation.
MEMBRANE-BASED WFI SYSTEMS
Most alternative designs to distillation have used one or two passes of RO, often with an ion exchange process and in virtually all cases, final polishing with UF or RO. The system designs over decades have been driven by practicality and regulation. The first alternative to distillation allowed by USP decades ago was RO. RO technology was generally not up to the task of consistent WFI performance and the technology did not flourish. Hot water sanitizable membranes did not exist and chemical sanitization was often inconsistent, allowing periodic microbial excursions beyond WFI specification. Some validated systems existed, but placements were few.
The presence of membrane systems was enhanced when the Japanese Pharmacopoeia allowed RO followed by UF as an alternative to distillation. Hot water sanitizable and continuous hot ultrafiltration elements were available and contributed to successful operation. Ultrafiltration had a lengthy, successful history in pharmaceutical manufacturing and was accepted. This technology change led to implementation of more systems that produced “WFI quality” water where pharmacopoeial WFI compliance was not required.
The change by USP to open WFI production to “distillation or a purification process proven to be equal to or superior to distillation” has helped to increase interest in membrane based WFI systems.
EP has created a monograph for Highly Purified Water with no process limitations and water quality specifications identical to WFI. This has helped to increase membrane system placement for production of “WFI quality” water.
Two-pass RO (TPRO), also known as product staged RO, was one of the earliest WFI membrane configurations. TPRO systems were more popular prior to the presence of conductivity and TOC tests. At that time the USP WFI monograph only allowed distillation or RO for process and it was accepted that the still or RO would be the terminal process. FDA had noted in The FDA Guide for Inspections of High-Purity Water Systems that if RO was used for WFI that two stages should be used to assure attainment of the quality specifications. TPRO can typically meet all of the required water quality parameters, but consistent attainment of Stage 1 conductivity can be an issue with some feed waters. TPRO systems often consist of a multi-media filter, softening, break tank, heat exchanger, hot-water-sanitizable activated carbon, prefilter, optional pH adjustment, 254-nm UV and two stages of hot-water-sanitizable reverse osmosis.
The implementation of a WFI conductivity test requirement and the liberalization of the USP WFI allowable processes increased use of systems implementing reverse osmosis, ion exchange processes and ultrafiltration or a final stage of RO. The logic of this type of system configuration is that the combination of reverse osmosis and ion exchange easily meet the conductivity and TOC specifications while the final ultrafilter or RO stage assures compliance with the endotoxin and microbial requirements. Systems of this type have had a lengthy history in production of “WFI quality water” prior to acceptance as a method to produce WFI to pharmacopoeial standards. The basic system capability for production of water with low contaminant levels has been long proven in other markets such as microelectronics for decades.
Most membrane based systems have several components that are either intermittently hot water sanitized or maintained continuously at a self sanitizing high temperature. Some systems have a final membrane stage that operates at the same elevated temperature as the storage and distribution system. Several systems of this type have been in operation for over ten years with water quality performance equivalent to distillation based systems.
A typical membrane based WFI system includes dechlorination, softening, a hot-water-sanitizable RO device followed by a hot water sanitized CEDI device. A continuous hot-water UF device polishes the water prior to storage and use as WFI if the water will be stored hot. A hot water sanitized UF or RO serves as the final stage if the product water will be stored at ambient temperature.
Advantages of using RO/RO or RO/UF to produce WFI are as follows:
- May be the lowest life cycle cost alternative
- Typically low energy requirements
- Typically very low conductivity, TOC, endotoxin and microbial levels
- Generally reliable operation
- Can be intermittently or continuously hot sanitized
- There is some history in the U.S. Pharmacopeia and Japanese Pharmacopoeia of using RO and UF for WFI
The most significant disadvantage is that EP does not allow a WFI production method other than distillation and therefore WFI membrane use is limited to non-EP applications. The history of membrane based WFI system usage is significantly less than with distillation, and this has negatively affected confidence in membrane systems among some pharmaceutical companies. Additionally, the RO system requires periodic cleaning, the membranes must be replaced at some point, and membranes can fail just as any technology has failure mechanisms.
Capital and operating cost comparison for distillation and membrane based systems is a key element of system choice when regulatory requirements do not dictate distillation only. This paper does not provide costs for several key reasons. Equipment specifications for materials of construction, instrumentation, control and other major cost factors impact capital costs significantly and capital costs are meaningless without detailed specifications. Operating costs are directly impacted by utility costs for water, wastewater, power, steam, chilled water and others and vary tremendously site to site. These costs are best based upon actual conditions case to case for accurate analysis. The significant possibility of lower life cycle economics for membrane based systems is based upon the relative absence of distillation based systems in non-regulated high purity applications.